Additives Masterbatch


About
Additive Masterbatch
Additive masterbatches are concentrated blends of several additives that are added to a polymer matrix to change or improve the final plastic product's characteristics. These masterbatches include functional additives or active substances that provide polymers with particular qualities, including flame retardancy, UV stability, antioxidant qualities, antistatic behavior, and more. They are used with base polymers (polyethylene, polypropylene, PVC, etc.) to enhance performance, durability, or processing qualities without changing the composition of the polymer as a whole.
The carrier resin melts and combines with the base polymer when heated and mixed mechanically, evenly spreading the active ingredients throughout the substance. Modern plastics manufacturing relies heavily on additive masterbatches, which provide useful enhancements like flame retardancy, antistatic behavior, UV resistance, and more. Concentrated is present in these masterbatches.
BENEFITS
Benefits of Additive Masterbatches

Improved Product Performance
Plastics may break down over time in the presence of sunshine due to UV radiation, which can cause color fading, brittleness, and strength loss. Particularly for outdoor applications like agricultural films, outdoor furniture, pipelines, and water tanks, UV stabilizers in masterbatches extend the life of plastic items by shielding them from the destructive effects of UV light.

Cost Savings
Additive masterbatches can lower the density of plastics in applications like foaming agents by incorporating gas bubbles into the polymer matrix. Because the finished product weighs less, this minimizes the amount of material required as well as the cost of delivery. By shielding plastic products from environmental deterioration, additives like UV stabilizers and antioxidants increase their use life. This lowers the long-term expenses for manufacturers and consumers by lowering the need for regular replacements.

Environmental and Sustainability Benefits
Additive masterbatches can give the polymer matrix biodegradable or compostable qualities, contributing to the movement toward environmentally friendly plastics. Certain masterbatches with additives enhance the properties of recovered polymers, facilitating material reuse without sacrificing quality. For instance, by stabilizing the polymer during reprocessing, additives can enhance the mechanical qualities of post-consumer recycled (PCR) materials.

Enhanced Safety and Protection
Lessen polymers' tendency to catch fire, assisting with the compliance of products with safety regulations in the electronics, automotive, and construction industries. Avoid the accumulation of static electricity, which can harm electronic components or explode in delicate areas like chemical processing plants. By preventing the growth of dangerous germs or fungi, medical devices, food containers, and other objects that are sensitive to hygiene can be protected.

Type Of Additive
Types of Additive Masterbatches
Masterbatch for antifog additives is a specialty mixture that keeps water droplets or fog from forming on plastic surfaces. When tiny droplets of condensation accumulate on a colder surface, it causes fogging, which disperses light and decreases transparency or visibility. Particularly troublesome is this impact in situations where unobstructed visibility is crucial, such as food packaging, greenhouse films, and optical lenses.
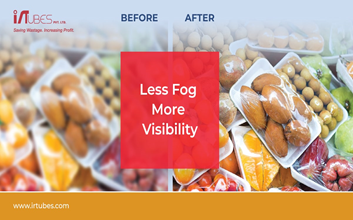
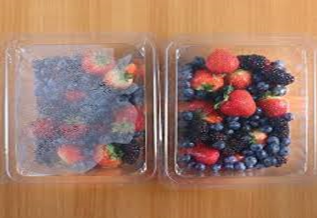
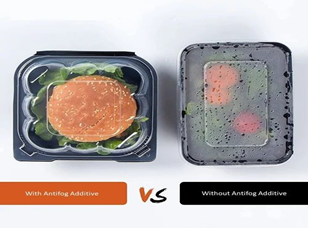
Antiblock additive masterbatch is used in the manufacturing of plastics to stop neighboring layers of films or sheets from adhering to one another, a process known as "blocking." When smooth plastic surfaces come into contact, blocking happens, especially when processing, storing, or handling the material. Without influencing transparency or mechanical qualities, the addition slightly roughens the plastic's surface or changes its surface characteristics to lessen the possibility of films adhering to one another.
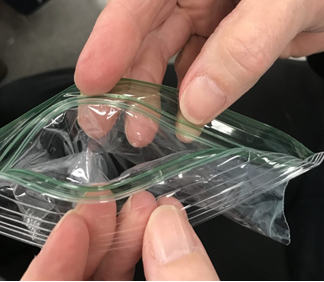
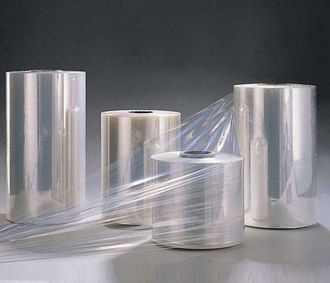
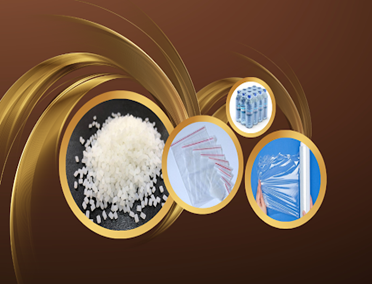
Masterbatch for antioxidant additives is a customized composition that is applied to plastics to guard against damage brought on by heat, oxygen, and UV light during production and product lifecycle. Outdoor films, industrial materials, automobile components, and food packaging are just a few of the many uses for these masterbatches. Manufacturers can enhance the mechanical performance, durability, and aesthetic appeal of plastic items by adding antioxidants to the polymer matrix. This will help the products last longer and use less material in the processing process.
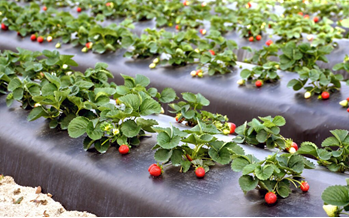
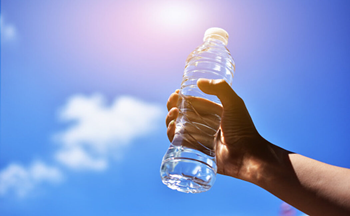
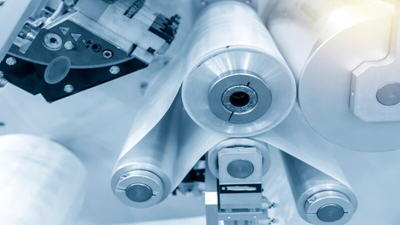
An anti-rodent additive masterbatch is intended to shield plastic products from harm brought on by rodents like mice and rats. Because they can cause expensive damage, interruptions to operations, and safety hazards, rodents are known to chew on plastic products such as cables, pipes, and films. To prevent rodents from nibbling on plastic objects, anti-rodent masterbatches contain certain compounds that repel them. Rat assaults can result in serious damage and safety hazards in a number of industries where these additives are employed, such as cables, pipes, automotive parts, and agricultural films.
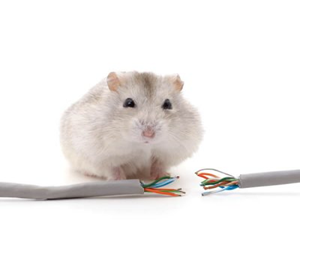

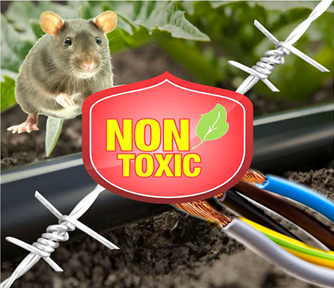
resilience against abrasion, surface scratches, and scuffs. Scratches, especially in consumer items, automotive parts, and packaging, can reduce the appearance, usefulness, and longevity of plastic products. Antiscratch additives assist in stopping surface degradation brought on by handling, regular usage, and exposure to the elements by hardening surfaces, decreasing friction, and producing smoother finishes.
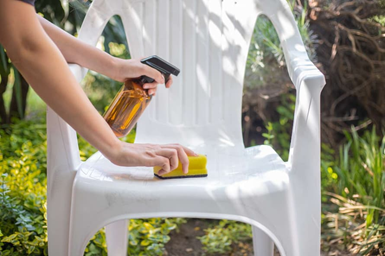
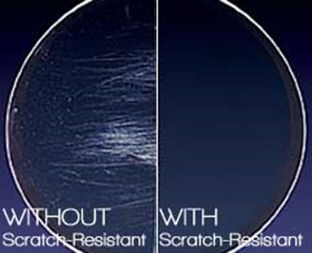

Antislip additive masterbatch is intended to lessen the slickness of plastic surfaces, enhancing the grip and averting slippage in a variety of applications. Antislip additives improve safety, functionality, and handling in items where slip resistance is crucial, like floors, films, automobile parts, and packaging, by altering the surface properties of plastic materials. The surface properties of plastic items can be altered by manufacturers to make them more stable, safer, and simpler to handle by adding additives like silicone compounds, mineral fillers, or waxes. Antislip additives are utilized in areas where slip resistance is essential for performance, safety, and product stability, such as packaging films and automobile components.
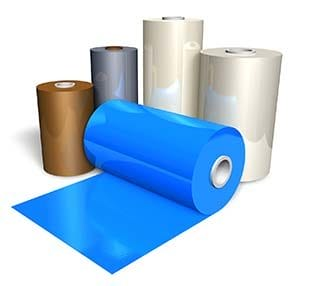
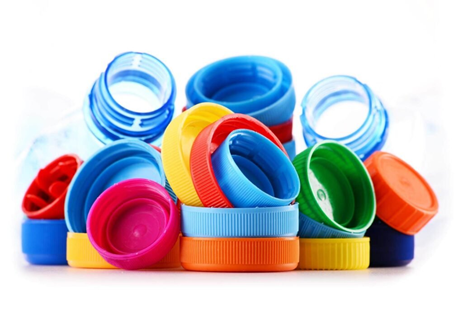
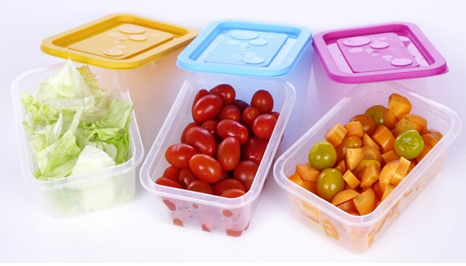
The purpose of the antistatic additive masterbatch is to minimize or completely remove the accumulation of static electricity on plastic surfaces. Because plastics are insulators, they are prone to static charge buildup, which can cause handling issues, dust attraction, electrical discharge, and even damage to delicate electronic components. Antistatic additives improve the performance of the material in applications where static electricity is an issue by dispersing these charges and avoiding static buildup.

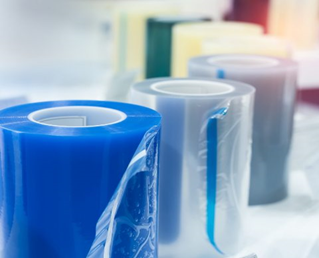

In order to prevent moisture-related problems in the final plastic product, such as bubbling, porosity, and surface flaws, a desiccant additive masterbatch is a particular formulation intended to absorb and remove moisture from polymer resins during processing. If moisture is left in raw materials, it can cause problems with quality, particularly in hygroscopic polymers like polyester, ABS, and polyamides (nylon). In order to provide a practical and efficient solution for moisture control, desiccant masterbatches include moisture-absorbing agents straight into the plastic during production.


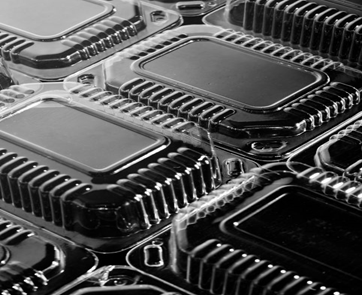
A flame retardant additive masterbatch is used to give plastic products flame resistance. These masterbatches include flame-retardant ingredients that aid in keeping plastic from igniting, slowing the spread of flames, and lowering the amount of smoke and harmful gases released during combustion. In many industries, especially those where fire safety is a major concern—such as electrical and electronic components, building materials, textiles, and automotive applications—flame retardant masterbatches play an important part.

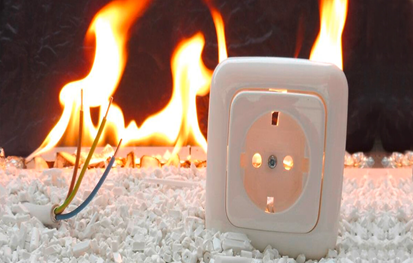

An anti-termite additive masterbatch is intended to shield plastic materials from termite damage and other wood-boring insects. These masterbatches offer a protective barrier for materials used in areas susceptible to termite infestations by containing active chemicals that either kill or repel termites. They are particularly advantageous in applications where plastics are utilized in contact with wood or in locations where termites are abundant, such as in building, packaging, and outdoor Products.

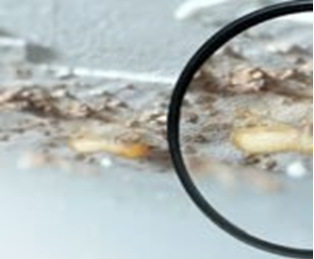

A modifier additive masterbatch is used to improve or change the characteristics of plastic materials during the processing and production phases. The physical, chemical, and mechanical properties of the base polymer are altered by the additions present in these masterbatches. They can enhance performance characteristics including adhesion, flexibility, impact resistance, and weatherability, enabling producers to customize the finished product to meet particular needs and applications.



By lowering friction and enhancing polymer flow during manufacture, lubricant additive masterbatch is a specific composition intended to improve plastic materials' processing properties and performance. The lubricating additives included in these masterbatches aid in the processing of plastics, giving the finished product smoother surfaces, better mold release, and higher mechanical qualities. Lubricant additive masterbatches are essential to the effectiveness of current plastic manufacturing processes. They also increase product quality and minimize equipment wear.



antibacterial qualities. The antimicrobial compounds present in these masterbatches prevent the growth of bacteria, fungi, and other microbes, improving the end product's hygiene and safety. They are especially useful in areas like food packaging, consumer goods, textiles, and medical devices where hygiene and cleanliness are essential. Antimicrobial masterbatches provide several advantages, such as improved cleanliness, longer shelf life, and durability. They are essential to modern manufacturing.
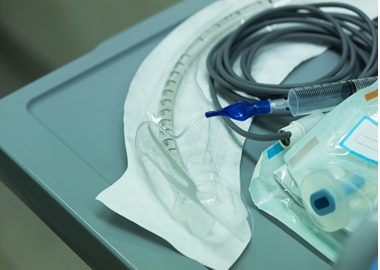
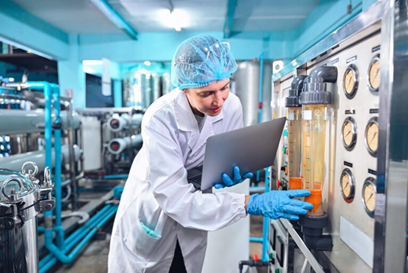
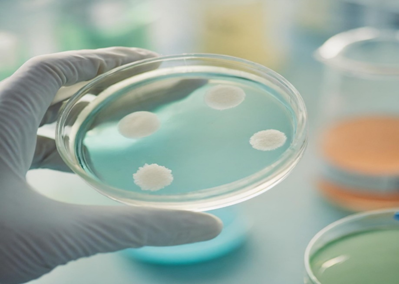
When the nucleating masterbatch is added to the polymer during processing, magic happens. The nucleating agents serve as templates as the molten polymer cools, promoting quicker and more consistent crystal formation. This causes the crystalline structure to become denser and more regular, which benefits the plastic in a number of ways. The nucleating additive masterbatch is a silent hero in the production of plastics. It functions in the background, accelerating crystallization, strengthening the product, increasing clarity, and cutting cycle durations.
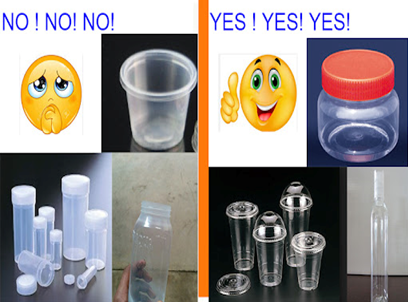

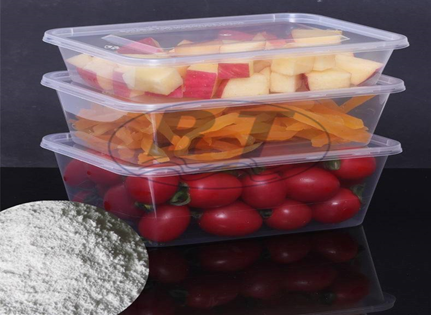
When the nucleating masterbatch is added to the polymer during processing, magic happens. The nucleating agents serve as templates as the molten polymer cools, promoting quicker and more consistent crystal formation. This causes the crystalline structure to become denser and more regular, which benefits the plastic in a number of ways. The nucleating additive masterbatch is a silent hero in the production of plastics. It functions in the background, accelerating crystallization, strengthening the product, increasing clarity, and cutting cycle durations.
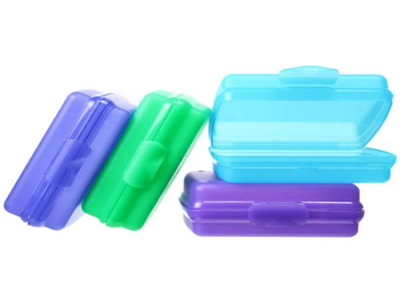
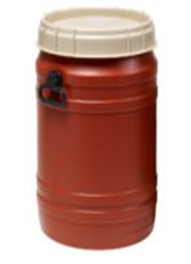
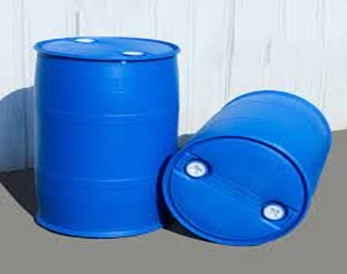
Optical brightener additive masterbatch is used to improve the whiteness and brightness of plastic products. Optical brightening agents (OBAs), which are substances that absorb ultraviolet (UV) light and reemit it as visible blue light, are present in these masterbatches. This optical effect improves aesthetics and amplifies the visual appeal of many plastic applications by making materials appear whiter and brighter than they are in their native form. With benefits such as enhanced aesthetics, increased product appeal, and versatility, optical brightener masterbatches play a significant role in modern production.



An oxi-biodegradable additive masterbatch is intended to improve the biodegradability of traditional plastic products. Oxo-biodegradable chemicals included in these masterbatches let plastics break down naturally over time and eventually transform into non-toxic products. This technique, which is frequently utilized in a variety of applications, including packaging, agricultural films, and single-use items, tries to solve the growing environmental concerns related to plastic waste. To achieve optimal performance in the end goods, considerations pertaining to regulatory compliance, degrading conditions, and compatibility are crucial.

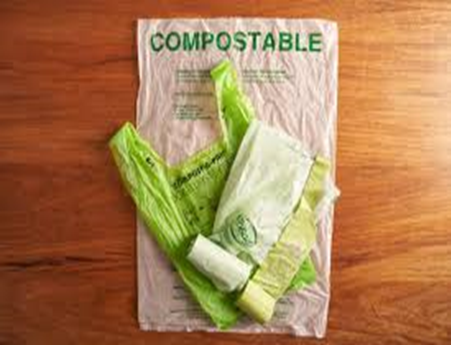
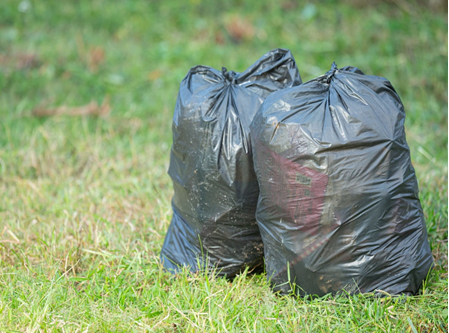
The purpose of the PPA (polyphthalamide) additive masterbatch is to improve the mechanical, chemical, and thermal resistance of thermoplastic materials. It is a specialty formulation. High-performance polymer polyphthalamide is renowned for its superior mechanical strength, chemical resistance, and thermal stability. PPA has the ability to greatly enhance base polymer performance when applied in masterbatch form, qualifying them for demanding applications across a range of industries.
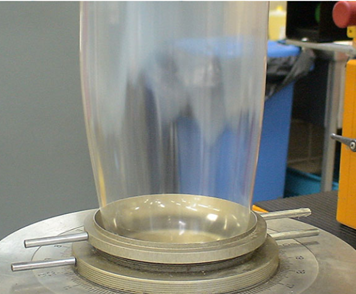

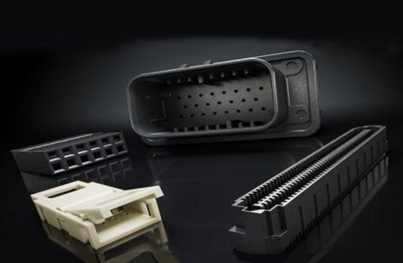
A slip additive masterbatch is used to improve the surface characteristics of plastic materials, especially to lessen surface friction. Slip additives, which are substances intended to lessen friction and enhance the ease of handling, processing, and end-use performance of plastic goods, are present in these masterbatches. Smoother surfaces, better processability, and higher performance in a range of applications can result from this. Slip additive masterbatches provide important advantages in contemporary plastic manufacturing, including better processability, decreased friction and abrasion, and improved surface characteristics.
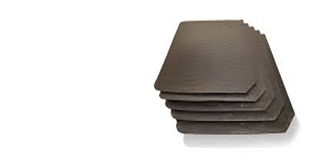
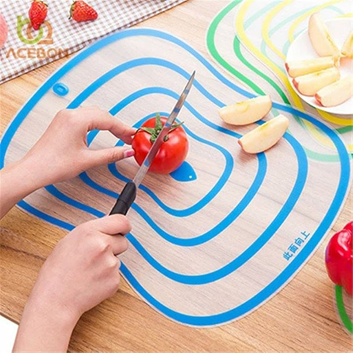
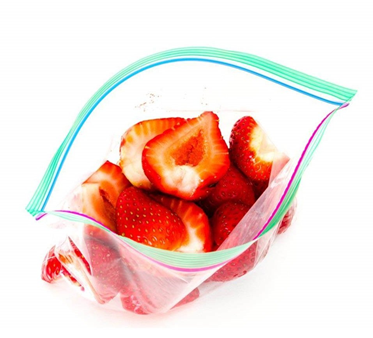
VCI (Vapor Corrosion Inhibitor) additive masterbatch is to prevent corrosion on metal surfaces while they are being stored and transported. VCI additives are substances that emit vapor-phase inhibitors to effectively stop rust and corrosion on metal surfaces when added to packaging materials or plastic products. Thanks to this technology, manufacturers and other companies that work with machinery, tools, and metal parts can save maintenance expenses and increase the longevity of their products. To maximize the efficiency of VCI additive masterbatches in real-world applications, however, factors including concentration levels, compatibility with other additives, performance testing, and regulatory compliance are crucial.
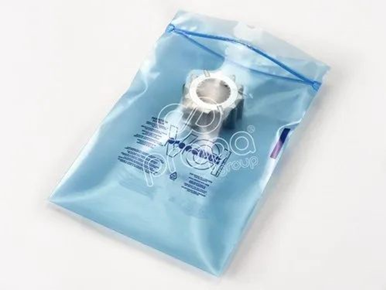


OUR PRODUCT SOLUTION FOR ADDITIVE MASTERBATCH
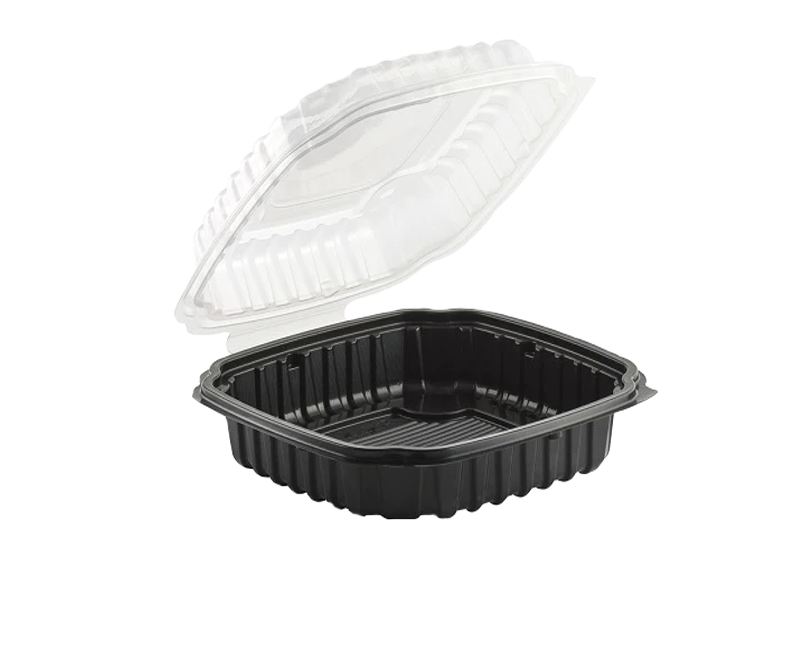
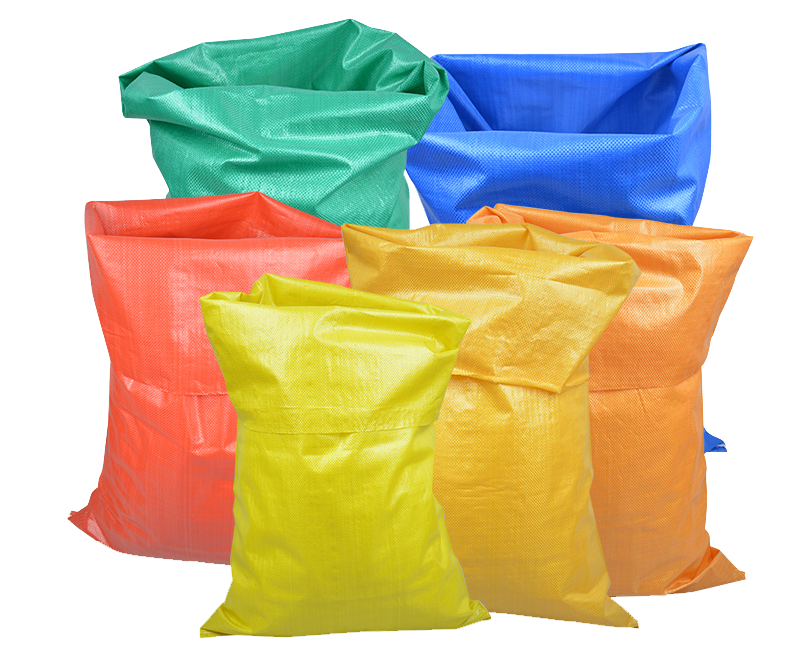
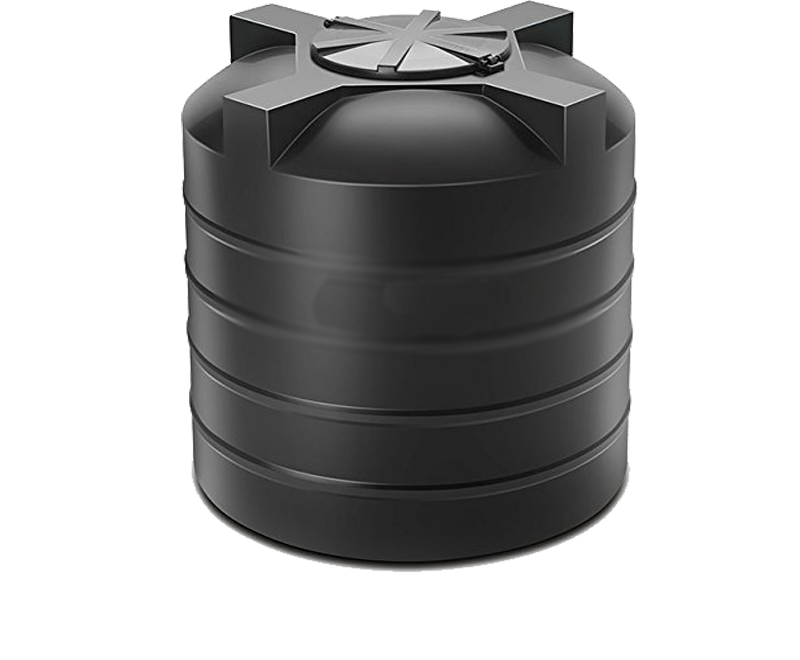
WATER TANK
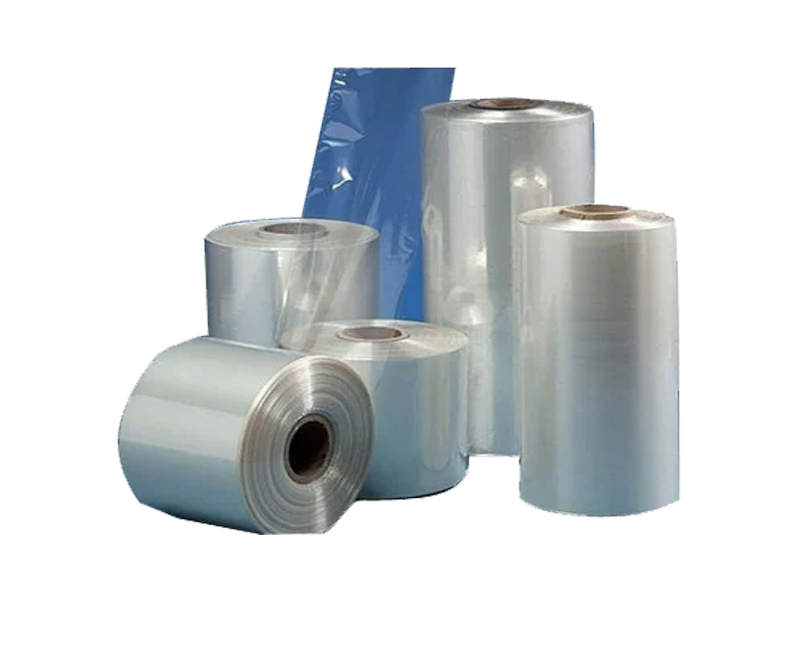
WOVEN SACK
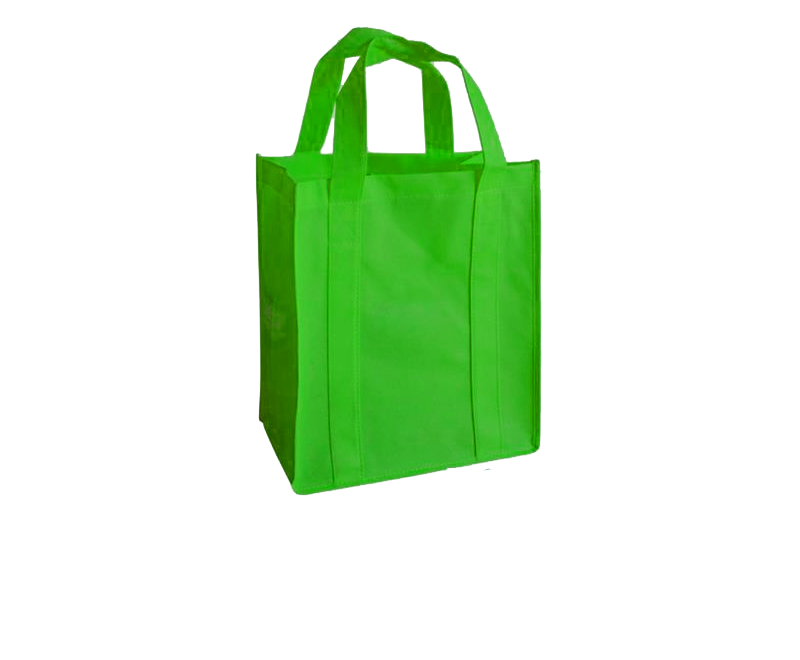
NON WOVEN
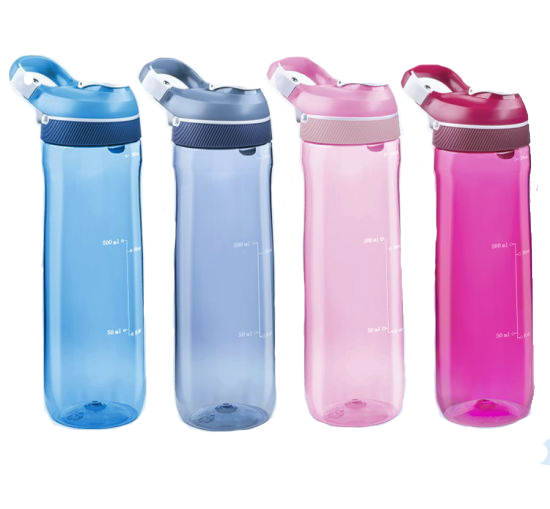