UV Masterbatch

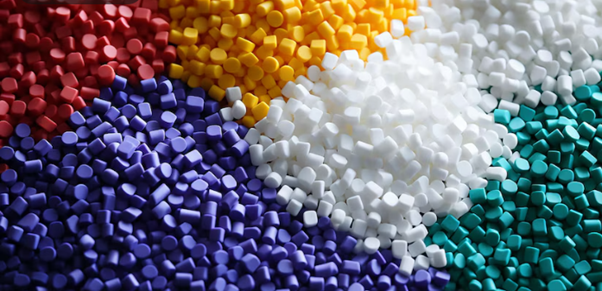
About
UV Masterbatch
UV Masterbatches are specialized additive concentrates that incorporate UV stabilizers into the polymer matrix to protect plastic products from ultraviolet (UV) radiation. When plastics are exposed to sunshine and UV radiation, these masterbatches are utilized to increase their longevity and durability. Over time, plastics may undergo degradation due to UV radiation, which can lead to embrittlement, discoloration, loss of mechanical capabilities, and general material deterioration. By absorbing or dissipating harmful UV rays, UV masterbatches assist prevent this and improve the performance and lifetime of plastic items in outdoor or UV-exposed conditions.
The stabilizers in UV masterbatches either absorb or block the damaging UV light that would otherwise penetrate deeper into the polymer during extrusion or injection molding. Benzotriazoles and benzophenones are examples of UV absorbers that collect UV light at the surface and transform it into a dissipated form of non-harmful energy, usually heat. A HALS, on the other hand, successfully "repairs" the damage before it results in degeneration by neutralizing the free radicals that arise when UV light breaks the polymer chains.
BENEFITS
Benefits of UV Masterbatches

Extended Product Lifespan
UV radiation can cause polymers to break down, leading to brittleness, cracking, and loss of mechanical strength. UV masterbatches shield plastics from these damaging effects, significantly extending their life, especially in outdoor applications.

Preservation of Mechanical Properties
UV exposure can lead to embrittlement, weakening the plastic's structural integrity. By using UV masterbatches, plastics maintain their flexibility, impact resistance, and overall mechanical performance over time.

Enhanced Thermal Stability
UV masterbatches often contain additives that also offer thermal stability. This ensures that the plastic not only resists UV damage but also performs better in environments with fluctuating or high temperatures.

Improved Appearance and Aesthetic Durability
UV rays can cause plastics to fade or yellow over time, especially in Coloured or transparent products. UV masterbatches protect the Colour and clarity of plastic materials, ensuring they retain their original appearance for longer.
Importance
Importance of UV masterbatches
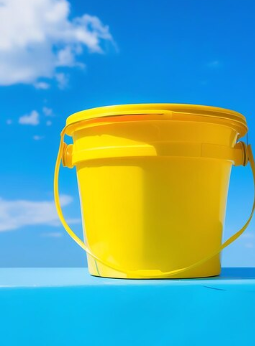
Injection moulding
UV masterbatches are essential for injection molding applications because they shield molded plastic parts from ultraviolet radiation. UV stabilizers are mixed into the basic polymer of these masterbatches during the molding process, assisting in preventing UV radiation-induced deterioration of plastic products. UV masterbatches are used in injection molding to shield components that are meant to be used outside or that will be under direct sunlight for extended periods of time.
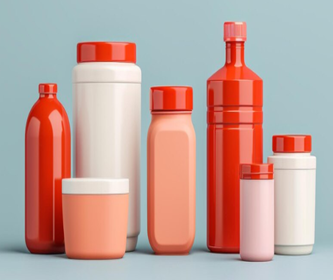
Blow Moulding
When making plastic items that need to be protected against ultraviolet (UV) light, blow molding requires the use of UV masterbatches. The presence of UV stabilizers in these masterbatches helps shield the plastic from deteriorating in the presence of light and other environmental elements.UV-resistant molded products appropriate for outdoor and UV-exposed areas. In addition to providing an affordable UV protection option, these masterbatches aid in maintaining the mechanical characteristics and visual attractiveness of blow-molded items.
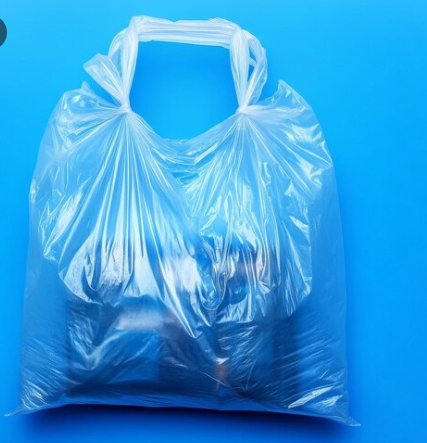
Woven Sack
The usage of UV masterbatches in the manufacturing of woven sacks, also known as woven bags, is growing, particularly for products meant for outdoor use or extended exposure to sunshine. UV stabilizers are incorporated into these masterbatches to shield the weaved sacks from UV radiation's harmful effects.These masterbatches provide an affordable way to extend the life of woven goods used in construction, packaging, and agriculture, among other industries.
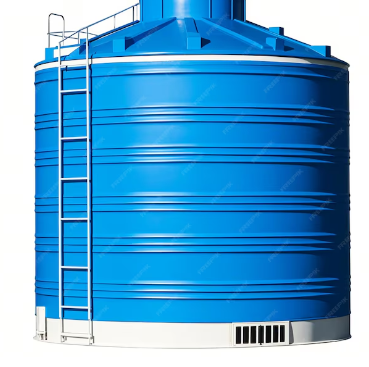
Water Tank
In the manufacturing of water tanks, particularly those composed of polymers like polyethylene (PE) and polypropylene (PP), UV masterbatches are indispensable. UV stabilizers used in these masterbatches shield the plastic from deterioration brought on by sunshine. During the molding process, UV stabilizers can be added to the polymer to create long-lasting, robust water tanks that can be used for residential, commercial, and agricultural purposes.
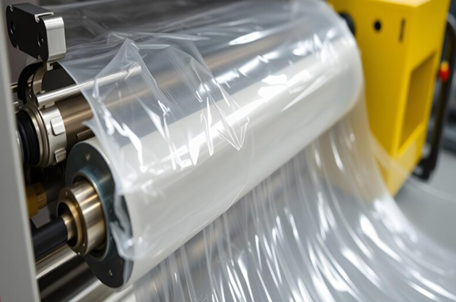
Blown Film
When manufacturing films that need to be protected from ultraviolet (UV) light, UV masterbatches are very important to the blown film extrusion process. One popular way to make plastic films is by blowing them out, which works particularly well for packaging. Blown films function better over time thanks to these masterbatches, which also help preserve their mechanical qualities, Colour, and general integrity.
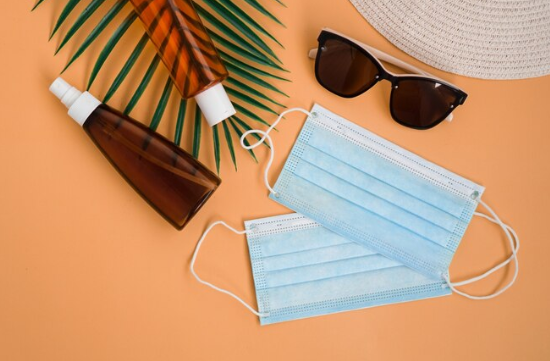
Non Woven Sack
In the manufacturing of non-woven bags, UV masterbatches are crucial, especially for situations where UV protection from outdoor exposure is required. Non-woven bags are extensively used in a variety of industries, including retail, packaging, and agriculture. They are usually constructed of polymers like polypropylene (PP) or polyethylene (PE).

Type Of UV
Types of UV Masterbatches
Described as substances that take up UV rays and transform them into heat to shield polymers from harm. Typical Types: Benzotriazoles: Excellent UV protection that works well for PE and PP. Benzophenones: Frequently utilized to preserve clarity in applications that are translucent or have a light hue.
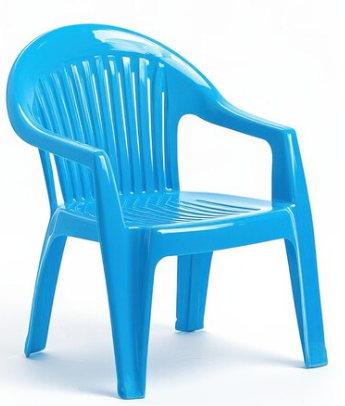

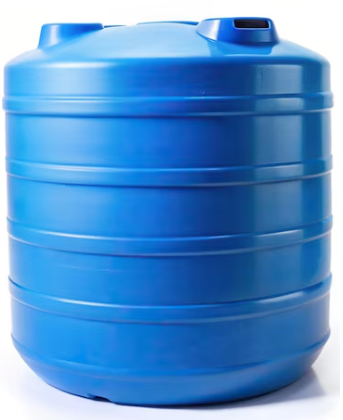
The purpose of stabilizers is to avert the oxidative degradation of the polymer by acting as radical scavengers.Mechanism: By scavenging free radicals produced by UV exposure, HALS stabilize the polymer instead of absorbing UV radiation.
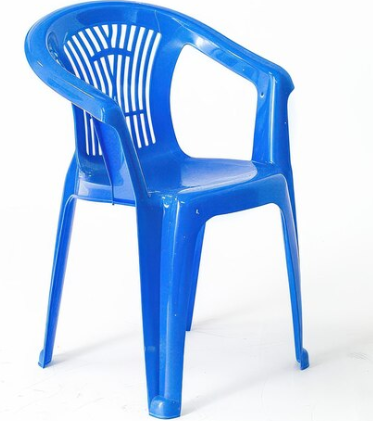
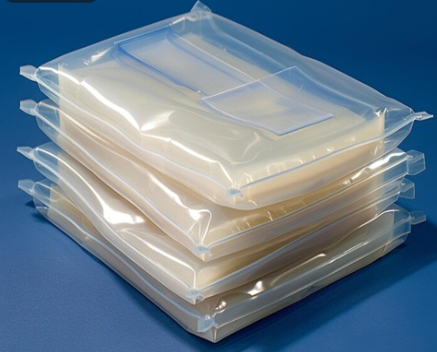
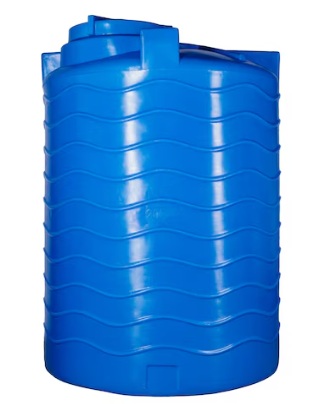
UV-blocking organic compounds that are frequently utilized in specialized applications.Examples include several organic dyes and pigments that absorb UV light.
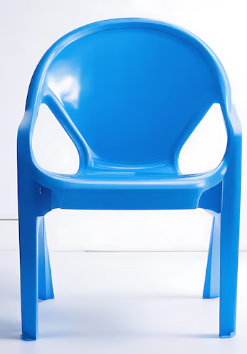

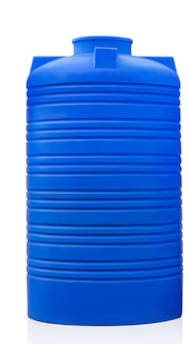
UV-protective mineral-based substances that are frequently utilized in formulations for improved thermal stability.Zinc oxide (ZnO) and titanium dioxide (TiO2) are two examples.

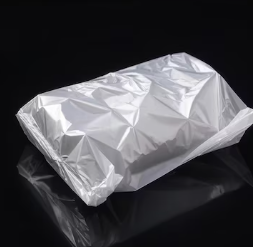
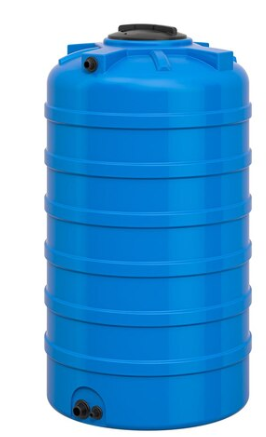
Solution For Agro Industries
UV Masterbatch Solution For Agro Industries
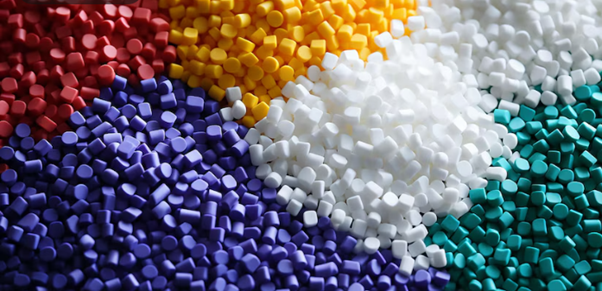
Unlocking the Potential of Agriculture with Plasmix Agro UV Masterbatches
UV masterbatches play a crucial role in enhancing the durability and performance of plastic products exposed to sunlight. Plasmix offers a range of UV masterbatches tailored to meet the specific needs of the agriculture industry, particularly in mulching film applications.
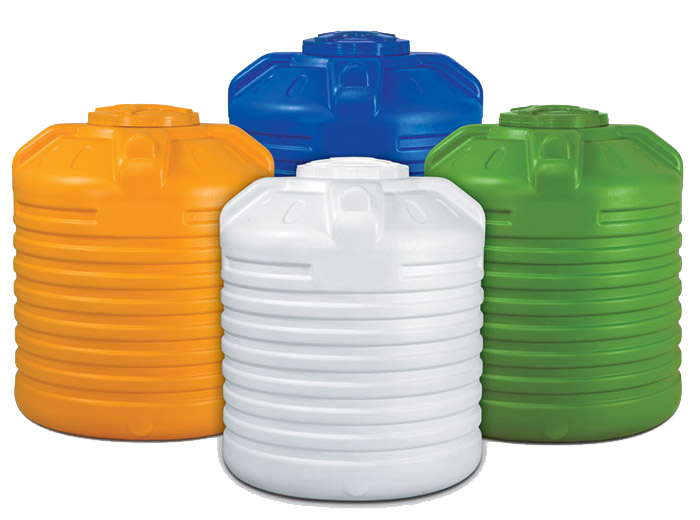
WATER TANK
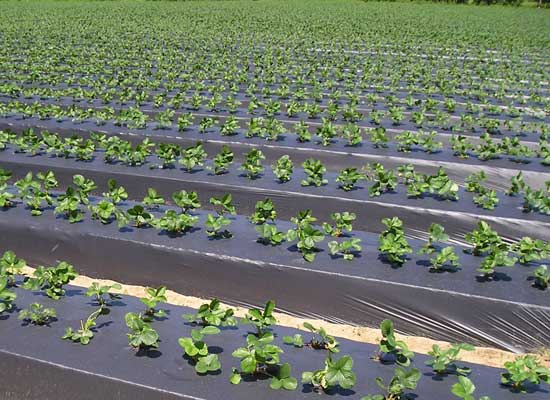
MULCH FILM
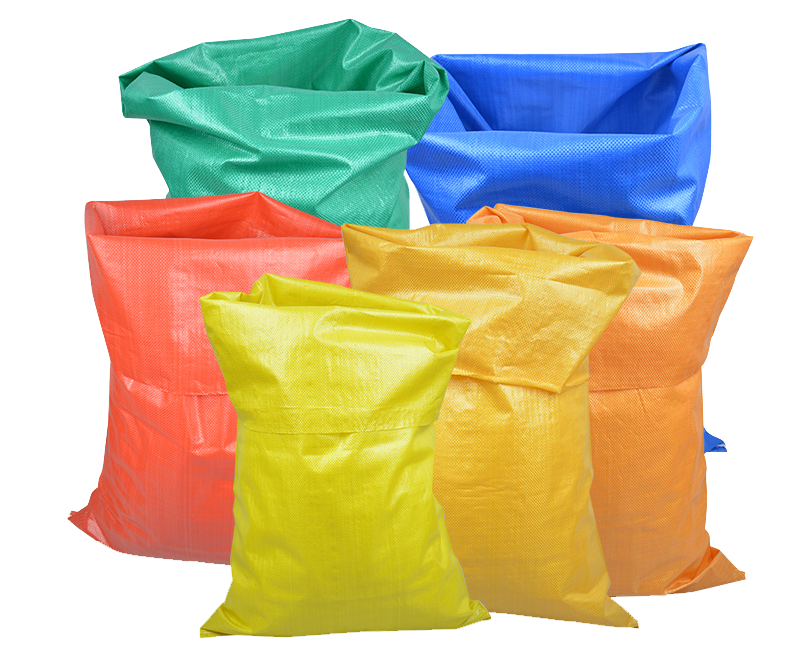
WOVEN SACK
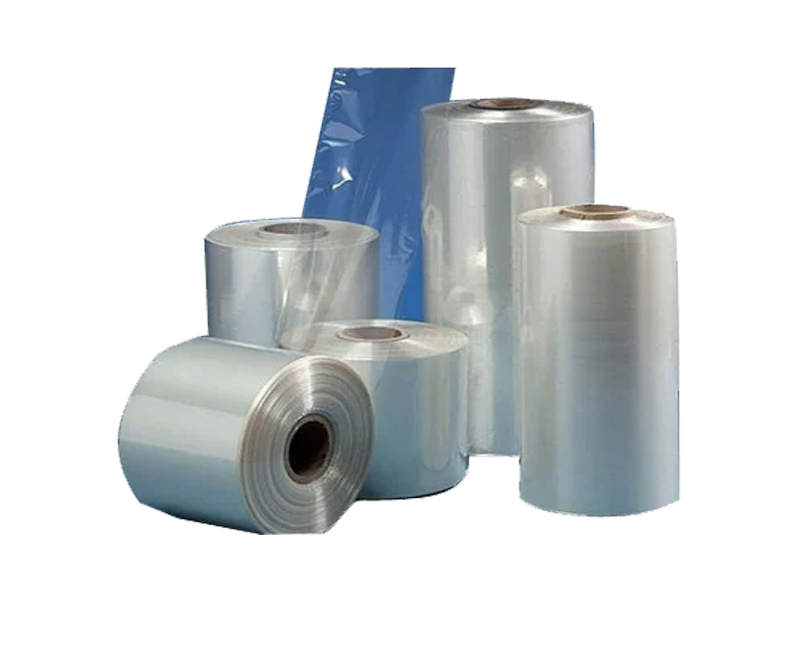
MULTILAYER
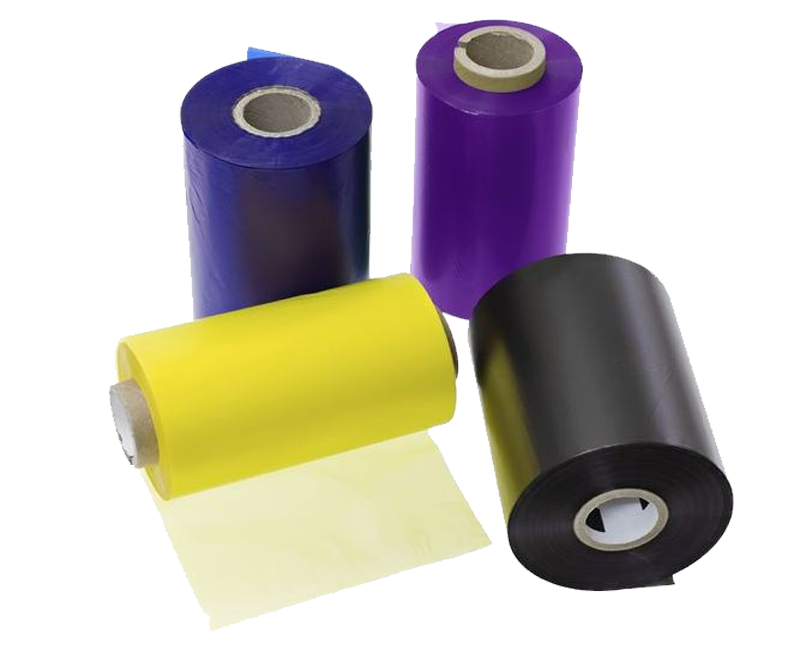