Filler Masterbatch

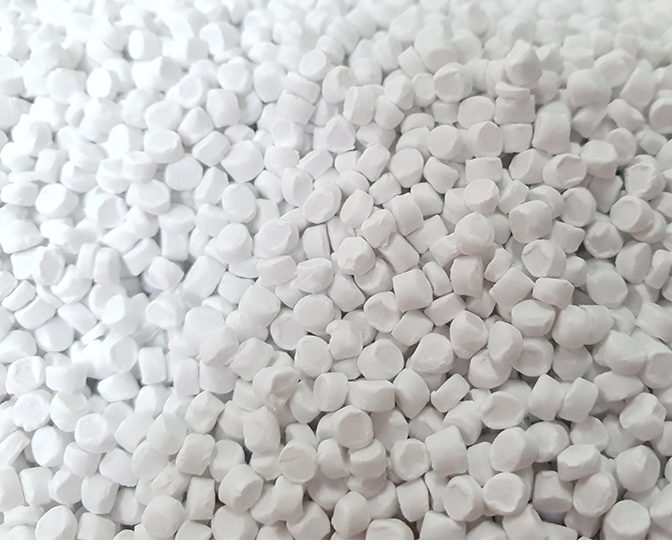
About
About Filler Masterbatches
In the plastics industry, filler masterbatches are specialty formulations intended to improve the mechanical and physical characteristics of polymers. They are made up of a polymer carrier with a high concentration of fillers, which can be additions like talc, barium sulfate,clay, calcium carbonate (CaCo3), or glass fibers.
Manufacturers can customize the qualities of their products to meet specific requirements by adding different fillers, which is why filler masterbatches are a crucial part of contemporary plastic manufacturing.
These masterbatches are intended to enhance the cost-effectiveness, stiffness, strength,and processability of the basic polymer.They are extensively utilized in a wide range of industries, including construction, automotive, and packaging, assisting manufacturers in meeting performance standards and maximizing material costs.
BENEFITS
Benefits of Filler Masterbatches

Enhanced Mechanical Properties
The addition of specific fillers, like glass fibers, enhances the material's impact strength, making it more resilient against physical stress. Fillers can also increase the tensile strength of plastics, enabling them to bear greater loads and resist deformation. Fillers improve the rigidity of the polymer, making it suitable for structural applications where strength is essential.

Heat Resistance
Fillers such as talc and certain mineral-based additives can improve the polymer's heat resistance, enabling it to be used in applications that are subjected to high temperatures.

Better Processability
During processing, filler masterbatches can improve the base polymer's flow properties. This enhancement may result in smoother extrusion and improved mold filling in injection molding, which will enhance surface quality and dimensional accuracy.

Opacity and Barrier Properties
Plastics' opacity is increased with fillers like titanium dioxide and barium sulfate,which is important for applications like packaging where light shielding is required.Specific fillers have the ability to improve the material's barrier qualities, shielding its contents from gasses and moisture.
IMPORTANCE
Importance of Filler Masterbatches
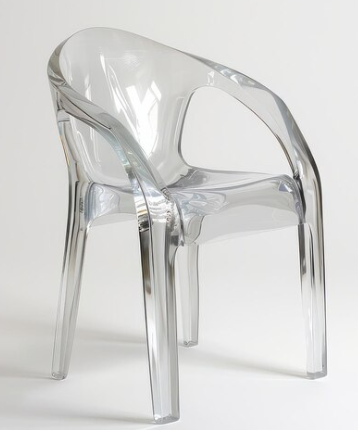
Injection moulding
Filler masterbatches play a vital role in enhancing the performance and properties of materials used in injection molding. By incorporating fillers, manufacturers can achieve cost savings, improve mechanical characteristics, and optimize processing. The careful selection and processing of filler masterbatches contribute significantly to the production of high-quality, durable, and cost-effective molded parts across various industries.
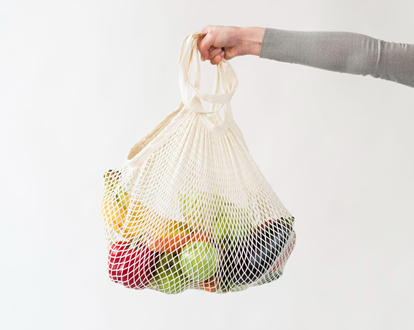
Woven Sack
The manufacturing of woven sacks, which are extensively used as packaging for things such as consumer goods, building materials, and agricultural products, frequently involves the usage of filler masterbatches. When it comes to improving the mechanical qualities, processability, and cost-effectiveness of woven sacks, filler masterbatches are crucial.
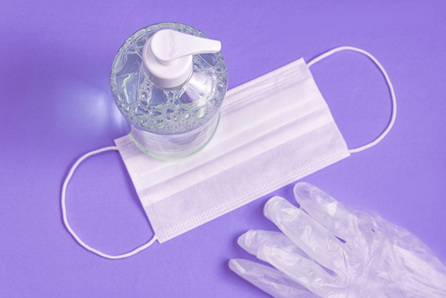
Non-Woven Sack
The manufacturing of non-woven sacks, which are frequently used for packing and transporting different products in sectors including retail, food packaging, and agriculture, requires a lot of filler masterbatches. In order to improve non-woven bags' mechanical qualities, lower production costs, and provide easier processing, filler masterbatches are essential.
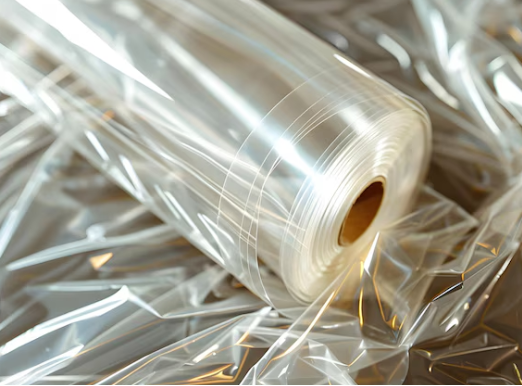
Blown Film
In blown film extrusion operations, filler masterbatches are frequently employed to boost productivity, cut expenses, and improve plastic film processing properties. Because they increase mechanical qualities, lower costs, and improve processability, filler masterbatches are essential to blown film extrusion operations.
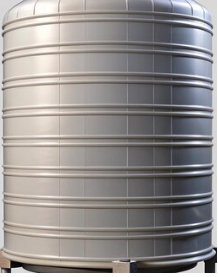
Water Tank
In the manufacturing of water tanks, especially those composed of plastics like polyethylene (PE) or polypropylene (PP), the filler masterbatch is an essential component. Manufacturers are able to improve the strength, durability, and cost-effectiveness of their water tanks by adding filler masterbatch.
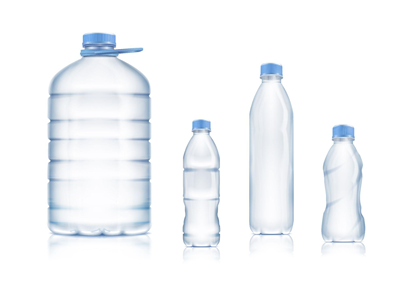
Blow Moulding
Filler masterbatch plays a vital role in the blow molding process, boosting the performance qualities and cost-effectiveness of plastic products. Hollow plastic items, such bottles, containers, and tanks, are frequently made via blow molding, mainly from polymers like polyethylene (PE) and polypropylene (PP).

TYPE OF FILLER
Types of Filler Masterbatches
Types of Filler
The main ingredient of PP Filler Masterbatch is polypropylene (PP), which is a carrier resin mixed with inorganic fillers like talc, calcium carbonate (CaCO3), or other mineral additions. In order to lower material costs and improve the mechanical qualities of goods based on polypropylene, it is frequently utilized in the plastics sector. The purpose of this kind of masterbatch is to enhance the overall performance and economics of the finished product by blending it with virgin PP during manufacturing.

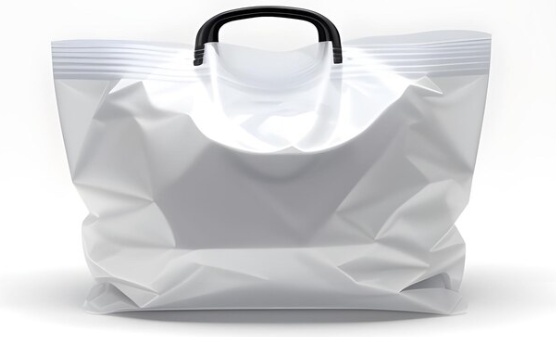

PE Filler Masterbatch is a concentrated blend of inorganic fillers, usually talc, calcium carbonate (CaCO3), or other mineral-based additives, with polyethylene (PE) serving as the carrier resin. It is widely employed in the plastics sector to lower total material costs, increase processing efficiency, and improve the physical characteristics of products made of polyethylene. The PE filler masterbatch is intended to be used with virgin polyethylene (LDPE, LLDPE, or HDPE) in production procedures including blow molding, injection molding, or extrusion.

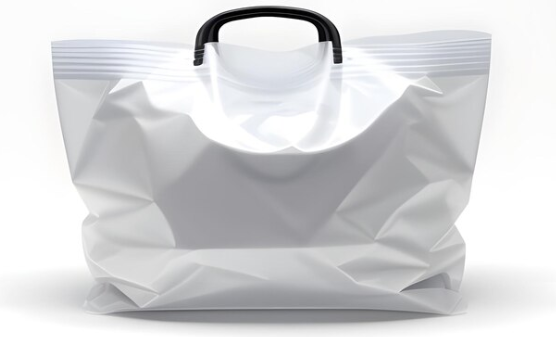
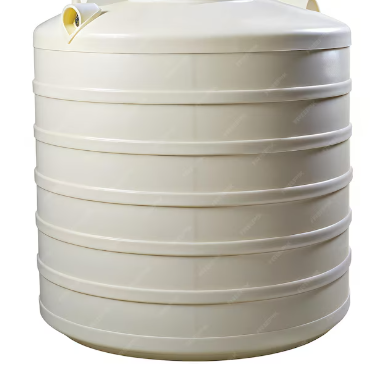
A polymer carrier resin, usually polyethylene (PE), polypropylene (PP), or another thermoplastic, is mixed with finely ground talc powder, a naturally occurring magnesium silicate mineral, to create Talc Filler Masterbatch, a type of plastic additive. By substituting talc for a portion of the base polymer, talc filler masterbatches improve the mechanical and physical qualities of plastic goods, increase processability, and lower the total cost of raw materials.

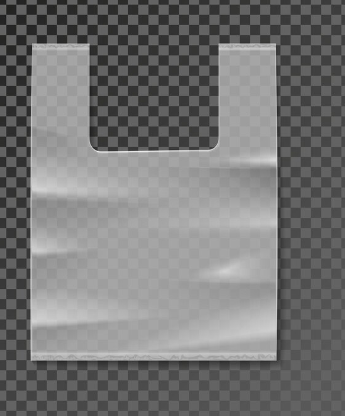

A polymer carrier resin such as polyethylene (PE) or polypropylene (PP) is mixed with finely powdered sodium compounds, such as sodium sulfate (Na₂SO₄) or other sodium-based minerals, to create Sodium Filler Masterbatch, a form of plastic additive. By partially substituting the base polymer, this masterbatch can be blended with virgin polymers during the plastic manufacturing process to improve specific physical qualities, improve processability, and drastically lower the final product's cost.

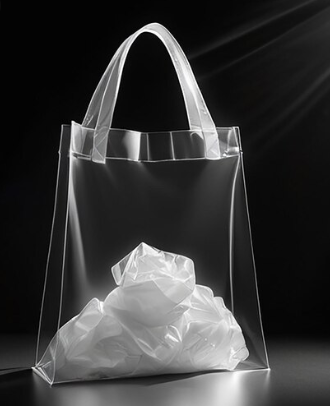

OUR PRODUCT
OUR PRODUCT SOLUTION FOR FILLER MASTERBATCH
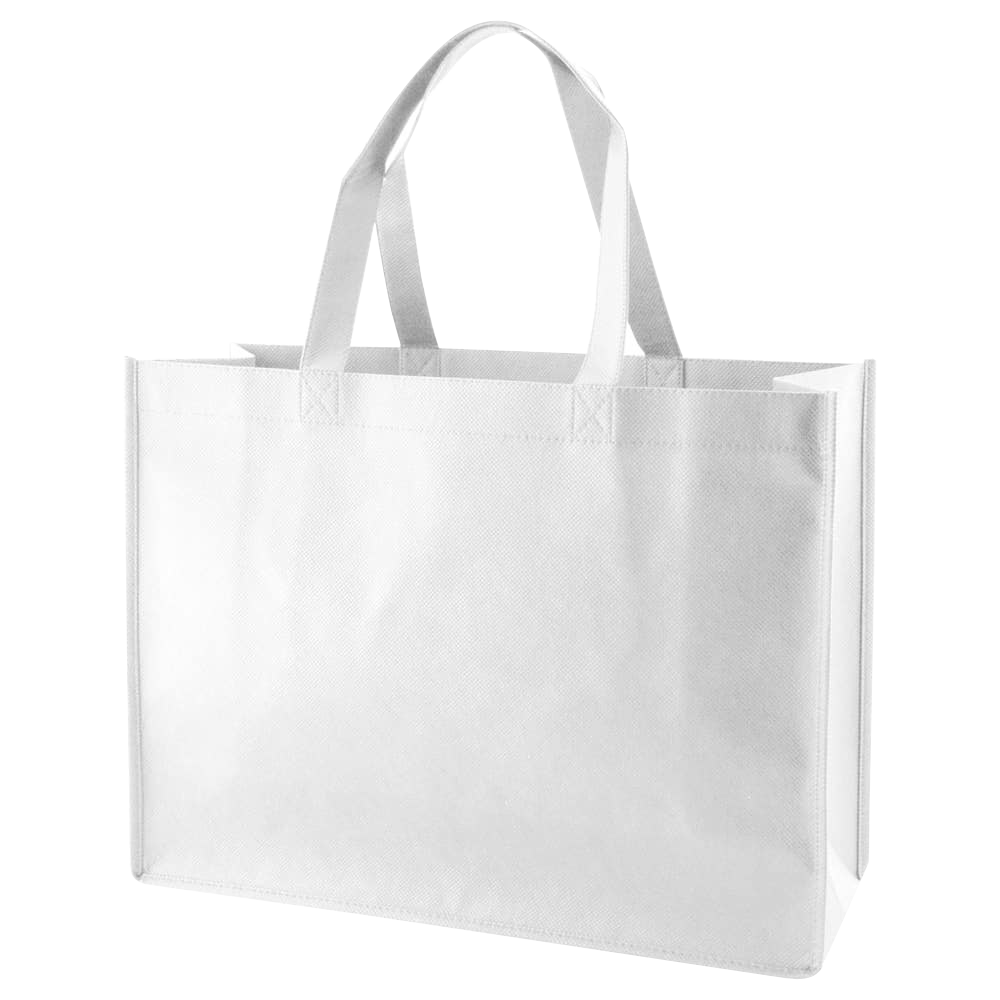
NON WOVEN
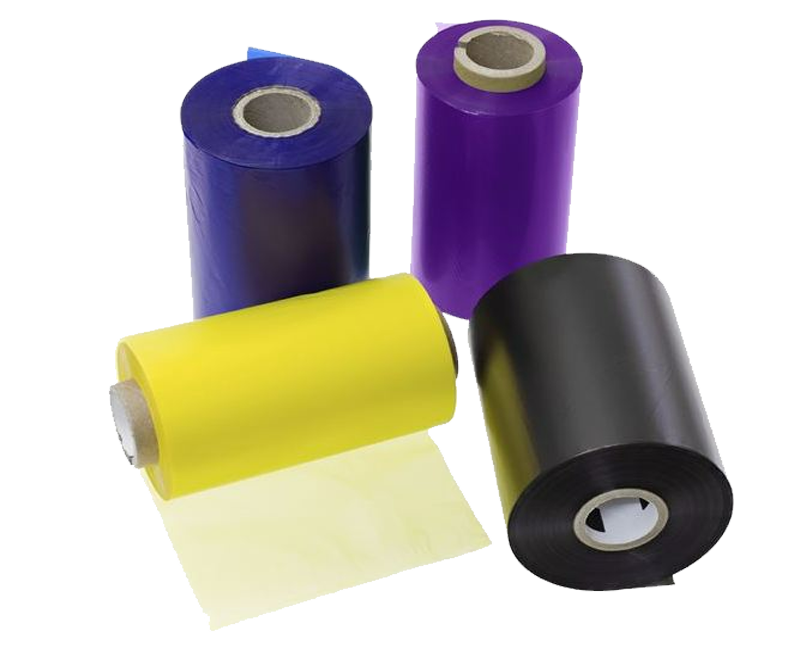
BLOWN FILM
WATER TANK
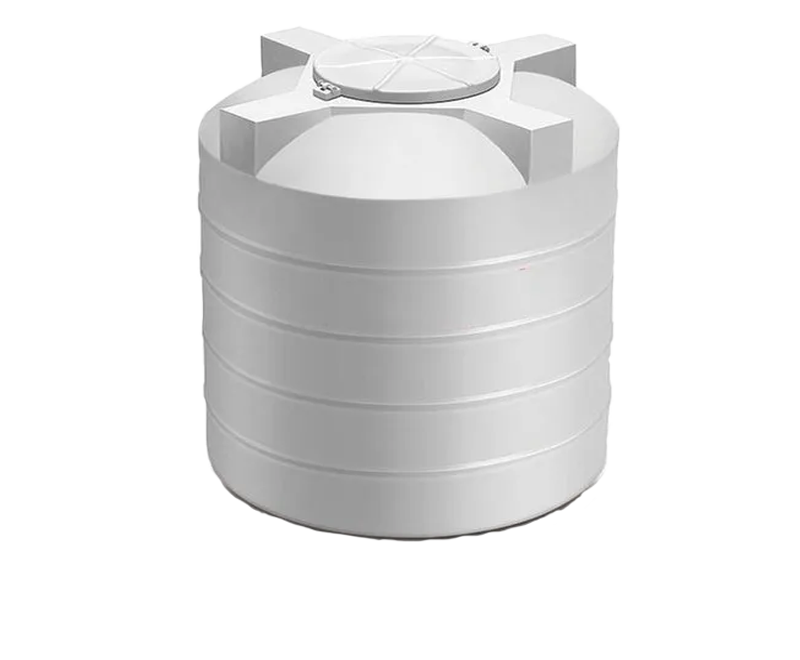